
La importancia del espesor en la pieza plástica
Pensemos por un momento en algún producto plástico, en su fabricación se crean lotes del mismo artículo en un solo turno de trabajo. Si observamos por ejemplo los envases de algún shampoo que compramos con frecuencia podemos notar que el espesor de las paredes de la pieza es regularmente uniforme, este particular punto es fundamental en el proceso de transformación del plástico mismo que de no tenerse en cuenta desde el análisis y diseño se traducirá con alta probabilidad en defectos y deformaciones, quebramientos, hundimientos o problemas en el color de la pieza final.
Por tanto, el espesor de las paredes del producto se convierte en una variable de suma importancia en el diseño particular del molde, a la par de la correcta fijación de variables del proceso para lograr el producto final deseado. El espesor de pared afecta fundamentalmente en la etapa del ciclo de inyección; a mayor espesor se requiere mayor tiempo de enfriamiento que puede derivar significativamente en la velocidad de producción, la cantidad de resina utilizada, la calidad y el costo de la pieza final. No hay restricciones para un espesor deseado, pero es recomendable diseñar siempre con el espesor más fino posible. En general dependerá del tamaño y geometría de la pieza de los requisitos estructurales y el tipo de resina a utilizar.
Es necesario estudiar los distintos materiales poliméricos y analizar cuál de ellos es conveniente para nuestro producto con relación al espesor requerido. El grosor de una pieza fabricada por inyección en general se encuentra entre los 2mm a 4 mm y una pared muy delgada puede presentar mediciones de 0.5mm. A continuación, se presenta un ejemplo de espesores recomendados.
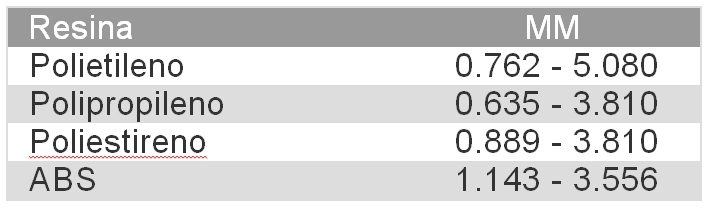
Un espesor más grueso se utiliza a menudo para dar mayor resistencia mecánica a una pieza. Sin embargo, esto puede generar efectos adversos ya que en dichas zonas se llegan a producir vacíos durante el enfriamiento debilitando al producto. Este problema se puede solucionar realizando una mejora del molde adicionando a la pieza costillas de refuerzo en zonas donde es posible.
Con respecto al color final requerido en cada igualación o desarrollo del pigmento, se debe conocer cuál es la pieza final y de ser posible obtener una muestra física con el fin de llegar al tono correcto; espesores de pared más fina o translucida requerirán una mayor concentración del color en su fabricación; por el contrario, espesores más gruesos necesitarán concentraciones de color más bajas. Con esto podemos entender que un mismo lote de masterbatch de un tono rojizo como ejemplo no presentara el mismo tono final en distintas piezas en particular por requerir mayor poder cubriente en los distintos espesores. El termoformado se puede usar como ejemplo; las piezas presentarán siempre tonos más intensos al inicio de realizarse el proceso, esto se debe en general al cambio en su espesor final y en la dilución del pigmento por esta etapa.
Podemos concluir que para realizar un desarrollo o igualación de un color en un producto plástico es indispensable que el laboratorio cuente con una pieza estándar de dicho producto o mínimo con la información técnica del mismo, pues el color y tono se ajustara en base a los espesores, el tipo de proceso y tipo de sistema del molde (colada fría o caliente). Esto determinara la correcta concentración y poder cubriente que deberán llevar los pigmentos en la formulación del masterbatch.