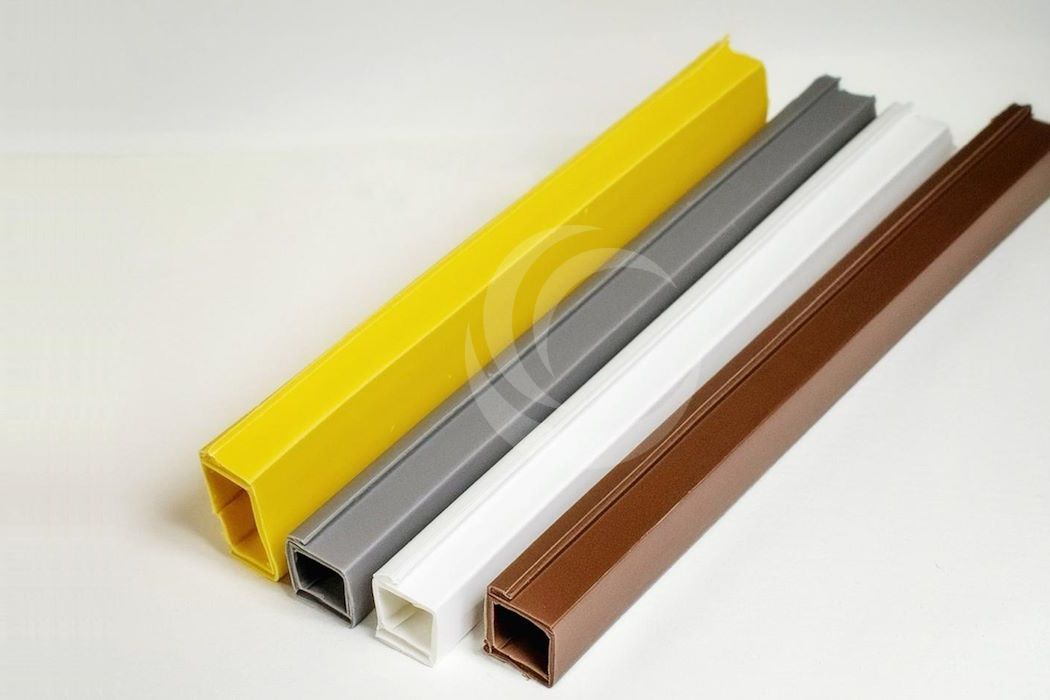
Insights de la fabricación de perfiles
Los perfiles de PVC tienen un gran potencial global, impulsado por innovaciones en formulaciones que incorporan aditivos para mejorar la resistencia a la luz y radiación solar. La fabricación de perfiles estructurales varía según su uso y ubicación. En México, estándares ambientales han limitado la difusión de perfiles para ventanas. Sin embargo, los perfiles para uso interior, como cancelería, puertas y persianas son ampliamente adoptados. Un uso destacado es la fabricación de muebles para jardín, que requiere compuestos con absorbentes de luz ultravioleta debido a su exposición exterior.
Es importante que estos productos no solo presenten una buena apariencia superficial para influir positivamente en la percepción del cliente durante la venta, independientemente de su ubicación final, sino que también mantengan sus propiedades funcionales a lo largo de su vida útil, incluso cuando están enterrados o instalados dentro de una pared. La evaluación meticulosa de la materia prima, las condiciones de proceso, el diseño de los equipos y la integración de aditivos son determinantes para la producción de perfiles.
En el proceso de coloración, algunos fabricantes prefieren el uso de masterbatch en lugar de pigmentos en polvo para asegurar una distribución homogénea. Los concentrados de color aplicados deben satisfacer diversas propiedades: buena resistencia a la intemperie para preservar la apariencia y durabilidad a lo largo del tiempo, estabilidad térmica para soportar altas temperaturas en la extrusión de plásticos técnicos como el policarbonato, y estabilidad química para prevenir reacciones adversas.
Durante la extrusión de perfiles, pueden surgir problemas superficiales como rugosidad y puntos, debido a desequilibrios en la fluidez entre la resina y el masterbatch, exceso de material recuperado, altas concentraciones de masterbatch, dispersión ineficiente de pigmentos y contaminaciones en la materia prima o en el equipo extrusor. Para resolverlo, se sugiere ajustar las propiedades de fluidez de la resina y el masterbatch, así como evaluar la dispersión del material recuperado. Además, un espesor uniforme del perfil ayuda a evitar puntos débiles que puedan comprometer su resistencia frente a alta presión, impactos o esfuerzos externos, para cumplir con propiedades mecánicas de flexibilidad, rigidez, resistencia al impacto, tensión y compresión según los requisitos específicos de cada aplicación.
Cuando el plástico fundido abandona el metal del dado en el equipo extrusor, se produce un efecto de hinchamiento debido a la liberación de presión en el cabezal. Este fenómeno afecta las dimensiones del producto en esta etapa y varía según parámetros como la velocidad de extrusión, la temperatura y el tipo de material. Al diseñar un perfil, es necesario considerar una salida más pequeña que las dimensiones deseadas del producto. En materiales como el PVC rígido, las dimensiones finales del perfil pueden reducirse hasta un 10% debido al efecto de hinchamiento. Por otro lado, los canales de flujo en el cabezal deben estar diseñados para equilibrar el tiempo de residencia del plástico con fricciones mínimas, previniendo el sobrecalentamiento y la degradación del material.
Para comprender completamente el funcionamiento de un proceso, es útil comparar la información actual con las condiciones anteriores al surgimiento del problema. El mantenimiento regular y una limpieza rigurosa de los equipos son también decisivos para asegurar un control eficiente de cualquier proceso de extrusión y prevenir problemas futuros.
• Expertos de Colorbatch.
• Blanco Vargas, R., 2008. “Diplomado en plásticos: Bases de la Extrusión”. Centro empresarial del plástico.
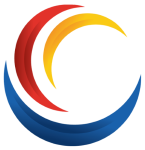