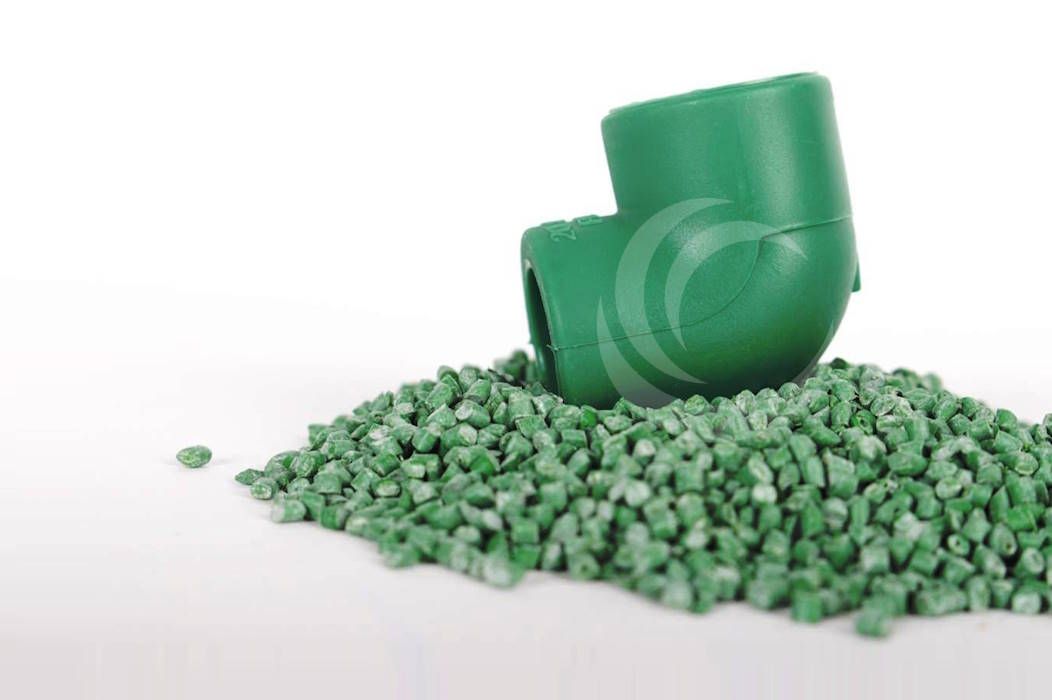
Dispersión de pigmentos en PVC
La dispersión efectiva de pigmentos es crucial en diversas aplicaciones industriales, desde la fabricación de tuberías de PVC hasta la producción de productos moldeados. Las tuberías de PVC rígido, se emplean comúnmente para uso hidráulico o aplicaciones sanitarias, en colores blanco, crema, gris, azul y verde, mediante el proceso de extrusión, mientras que las conexiones se obtienen por inyección o termoformado.
El éxito de la dispersión, y por ende del uso del pigmento comprende varias etapas: humectación, molienda, distribución y estabilización. Comenzando con una premezcla adecuada de todos los componentes para asegurar una distribución uniforme de las partículas de pigmento en el plástico.
En la humectación la resina entra en contacto con los aglomerados de pigmento, promoviendo la separación inicial de las partículas. Se busca el contacto total entre la superficie del pigmento y la resina, desplazando el aire y preparando las partículas para las siguientes etapas del proceso de dispersión. La efectividad de la humectación varía según la polaridad de la superficie del pigmento y la naturaleza de la resina.
La molienda reduce el tamaño de las partículas de pigmento y desintegra los aglomerados, asegurando su distribución uniforme en el material plástico para una coloración consistente y atractiva. Superar las fuerzas de cohesión de los aglomerados requiere energía, especialmente para lograr una dispersión fina. En la etapa final, las partículas dispersas se estabilizan para evitar la re-aglomeración y mantener una distribución uniforme.
Para simplificar el proceso de dispersión, muchos fabricantes utilizan masterbatch, ya que se mezclan fácilmente con la resina, garantizando una distribución homogénea del pigmento y resultados consistentes con una dosificación del 2% al 4%, según la concentración del pigmento.
La maquinaria utilizada para la dispersión varía desde equipos discontinuos hasta continuos, adaptándose a diferentes necesidades. En la coloración de PVC rígido y plastificado, se destaca el uso del mezclador rápido, que con su rotación rápida rompe aglomerados y dispersa los pigmentos en la resina, seguido del aprovechamiento de energía obtenida por medios mecánicos como la cizalla o el impacto en procesos como la extrusión.
Estas fuerzas de cizallamiento aumentan con la viscosidad de la resina fundida, la cual puede reducirse mediante la disminución de temperatura. Sin embargo, una temperatura más baja no favorece la humectación óptima del pigmento en la resina. Optar por una temperatura intermedia entre la ideal para la humectación y la que proporciona un buen cizallamiento conlleva a un fracaso en ambos aspectos, resultando en una dispersión deficiente.
Para lograr una coloración uniforme en un material plástico, no basta con humectar y desagregar los pigmentos; también se requiere una distribución homogénea de las partículas pigmentarias en la resina. A menudo, cuando se utiliza masterbatch, se confunde una mala distribución de las partículas con una dispersión deficiente, lo cual puede deberse a un tiempo de mezcla insuficiente.
Una recomendación final para considerar en el proceso de transformación del PVC es que absorbe menos del 0.02% de agua en 4 horas a temperatura ambiente. Esto posibilita el procesamiento del material sin necesidad de un secado previo, aunque se debe limitar el material remolido al 20% en combinación con material virgen para mantener su estabilidad térmica y capacidad de flujo. Cada ciclo de reprocesamiento disminuye estas propiedades, a menudo requiriendo reformulación con estabilizadores y lubricantes adicionales. Para purgar la maquinaria, se utiliza polietileno, ABS o acrílico, evitando el acetal o nylon debido a reacciones adversas con el PVC.
• Expertos de colorbatch.
• Blanco Vargas, R. (2008). Modulo 3. Bases de la Extrusión. Centro Empresarial del Plástico.
• Gili Bas E. 1990, Coloración de materias plásticas, España, Centro español de plásticos.
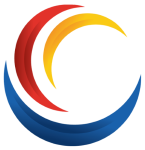