
Deformación en la inyección de envases y embalajes para alimentos
Un buen envase y embalaje para alimentos debe proteger su textura, aroma y sabor, prolongando su vida útil y garantizando seguridad, calidad y satisfacción del consumidor. Debe ser eficaz contra microorganismos, polvo y humedad, asegurando un sellado adecuado para evitar derrames y minimizar el riesgo de contaminación. Es por eso que la elección del material y el diseño son fundamentales para mantener la estabilidad dimensional y la resistencia del envase, ya que factores como el encogimiento pueden afectar su funcionalidad y comprometer tanto la calidad del producto como la experiencia del consumidor.
En relación con lo anterior, el alabeo o warpage se presenta como un defecto en los productos moldeados por inyección, especialmente en piezas grandes y planas, como tapas de contenedores de alimentos. Es observable, por ejemplo, cuando una tapa no se mantiene estable sobre una superficie lisa. Este problema surge debido a la contracción desigual del material durante la fase de enfriamiento en el proceso de inyección. lo que genera curvaturas o torsiones. Las tensiones internas resultantes afectan la integridad del producto, aumentando el riesgo de daños durante transporte y almacenamiento, impactando así en su vida de anaquel y en la seguridad del consumidor.
Las causas del alabeo pueden atribuirse a múltiples factores relacionados con el molde, la máquina, el proceso, el diseño del producto y el material.
Dentro de los materiales más utilizados en envases para alimentos se encuentran el PP y el HDPE, que se caracterizan por ser anisotrópicos, es decir, tienen variación de las propiedades físicas en diferentes direcciones. Al moldearlos por inyección, es probable que el flujo del material oriente las moléculas de manera diferente en los ejes X, Y, y Z, de la pieza provocando una contracción desigual que puede generar tensiones internas, deformaciones y alabeo.
Además, su estructura semicristalina, compuesta por zonas cristalinas (ordenadas) y amorfas (desordenadas), les otorga rigidez y flexibilidad, pero también los hace propensos a una contracción irregular durante la fase de enfriamiento. Las zonas cristalinas se solidifican a temperaturas más altas que las amorfas, lo que provoca diferencias en la contracción del producto al enfriarse, aumentando el riesgo de deformación.
Este fenómeno se ve acentuado por el uso de un masterbatch mal formulado para la coloración. Algunos pigmentos alteran la viscosidad de la resina durante la inyección, dificultando el llenado uniforme del molde y provocando contracciones desiguales. Aunado a esto, ciertos pigmentos modifican las propiedades térmicas de la resina, provocando tensiones internas durante la etapa de enfriamiento de la pieza final. Los masterbatch con altas concentraciones de pigmentos también pueden afectar la distribución del material, contribuyendo a que se pierda la forma original.
Por otro lado, parámetros inadecuados en el proceso de fabricación, como la presión, temperatura y flujo, junto con un diseño deficiente del molde que cause enfriamiento desigual y variaciones en el grosor de la pieza, generan tensiones internas que afectan su estabilidad dimensional. Incluso condiciones como temperaturas desiguales en el molde y el núcleo, presión de mantenimiento incorrecta, ciclos de moldeo demasiado cortos o velocidades de llenado y expulsión inapropiadas pueden agravar la contracción desigual.
La geometría de la pieza también desempeña un papel crucial: variaciones de espesor y una ubicación incorrecta de las compuertas —por donde entra el material— pueden generar flujos irregulares, aumentando las tensiones internas. Igualmente, refuerzos mal distribuidos en envases tipo caja pueden intensificar el problema. Finalmente, un funcionamiento inadecuado de la máquina, como eyectores desequilibrados o una apertura asimétrica del molde, contribuye aún más a las deformaciones.
Como se mencionó anteriormente el alabeo puede presentarse en piezas pequeñas, aunque es más frecuente en piezas grandes, pues su tamaño favorece el enfriamiento desigual. Por lo tanto, puede prevenirse con un enfoque integral que considere:
- Selección adecuada de materiales: Tanto la elección de la resina como cualquier aditivo, asegurando el cumplimiento a normativas de seguridad alimentaria.
- Uso de agentes nucleantes: Añadir un agente nucleante adecuado acelera la cristalización de la resina y mejora el enfriamiento, reduciendo las diferencias de contracción. Es crucial que el agente sea compatible con el proceso para evitar complicaciones.
- Proveedor de masterbatch: Es importante especificar claramente los requisitos al proveedor, brindar retroalimentación sobre problemas previos en la fabricación y el desempeño del masterbatch durante las pruebas acompañado de controles de calidad. Esto optimiza la formulación y garantiza la compatibilidad con la resina y las condiciones del proceso.
- Ajuste de parámetros de inyección: Aumentar la presión y el tiempo de inyección cuando sea necesario, garantizando una temperatura uniforme en el barril y el molde.
- Optimización del Diseño y Moldeo: Revisar la ubicación de las compuertas de inyección, garantizar espesores uniformes y un sistema de enfriamiento equilibrado.
- Mantenimiento preventivo: En las máquinas de fabricación para asegurar su correcto funcionamiento y evitar fallos durante el proceso de moldeo.
Un control riguroso de estos aspectos minimiza errores y garantiza que el consumidor reciba un envase funcional y seguro que cumpla con sus expectativas.
• Expertos de colorbatch.
• Mexpolimeros (s.f) ¿Por qué los plásticos se encogen?
• Young L., 2024, Análisis del alabeo y soluciones | Defectos del moldeo por inyección, First Mold.
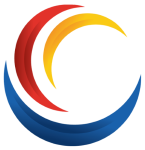