
¿Cómo evitar la saturación de color en un envase plástico?
Hoy en día encontramos una gran variedad de envases de plásticos que sirven para almacenar, transportar, comercializar de manera sencilla, rápida y segura una amplia gama de productos. A estos atributos de utilidad deben adicionarse dos factores clave en su comercialización; el color del envase que en conjunto con el diseño ergonómico se convierten en “vendedores silenciosos” que se destacan en los anaqueles. En el caso del color, su peso específico cobra relevancia desde la perspectiva de la mercadotecnia del producto y es aquí donde la calidad del “coloreado” se relaciona de forma directa con la pigmentación obtenida del masterbatch utilizado.
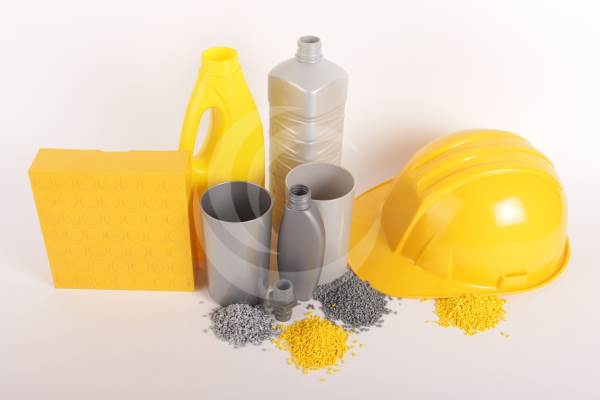
Para realizar una adecuada formulación de color debemos contar con toda la información técnica y comercial, como es el tipo de producto final en el que se va a aplicar el masterbatch o pigmento, así como todos los datos y especificaciones técnicas.
Por otra parte, se requiere desarrollar un proceso estandarizado (temperaturas de las distintas zonas, tiempo de residencia, RPM del usillo, alimentación del masterbatch), seleccionar la resina a utilizar y cumplir estrictamente las normativas de este. Cabe destacar, como lo hemos descrito en articulo previo, el espesor del envase.
Una vez recolectada la información del producto podemos iniciar la formulación, previo a un análisis técnico, esto con la finalidad de desarrollar la mejor alternativa de color y evitar problemas como la saturación del envase durante el proceso.
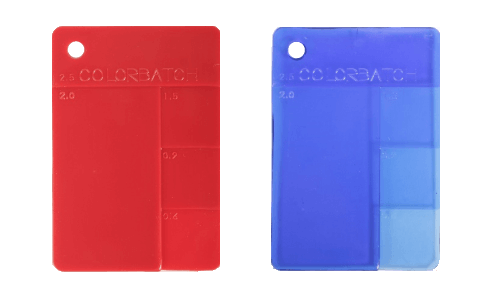
Recomendaciones para no saturar el envase plástico:
- Asegurar la homogenización del masterbatch con la resina.
- Largo y diámetro del pellet, es importante estandarizar las medidas de los pellets ya que se corre el riesgo de que en algunas partes de la botella pueda presentar mayor coloración. Para esto debemos cuidar la calidad geométrica de nuestros pellets ya que, si es muy chico, grande, doble, triple, en otra forma como lenteja, flakes o amorfo esto puede provocar que se inyecte menos o más color en nuestras botellas.
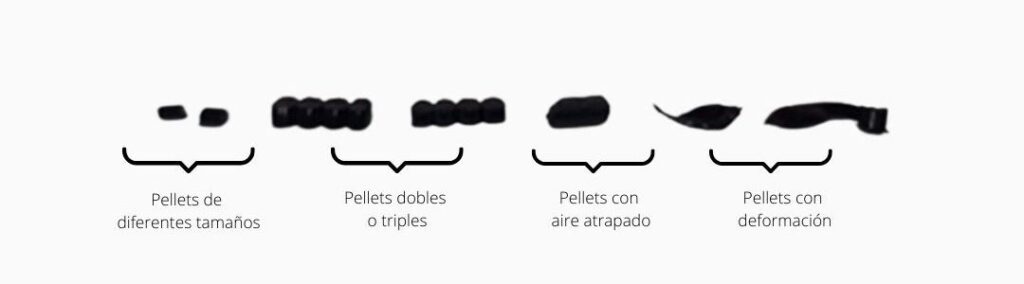
- Libre de grumos: estas impurezas o mala dispersión que se puede presentar en el masterbatch pueden afectar el acabado de nuestro producto final.
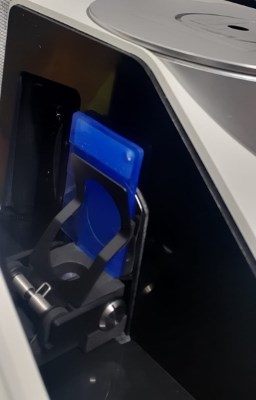
- Humedad: cuando el pellet contiene un alto porcentaje de humedad estropea la estética del producto presentándose como puntos blancos (ojos de pescado).
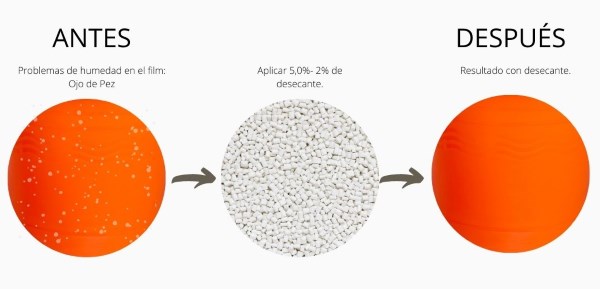
- Cuidar la naturaleza de los pigmentos a usar (orgánicos e inorgánicos esto dependerá de las normativas que deberá cumplir: No toxico, CONEG y FDA).
- La aplicación del masterbatch va del 0.5 al 5% dependiendo de las necesidades de cada cliente.
- Un espectrofotómetro resulta de gran ayuda ya que podemos determinar Deltas de color, reflectancia, absorbancia y opacidad. Para ampliar más estos conceptos te invito a leer el siguiente blog “Cuando utilizar el respaldo blanco para evaluaciones de color por el transformador de plástico”.
Para concluir con este interesante tema, debemos ser cuidadosos con la selección de nuestro masterbatch y estandarización del proceso, para obtener los resultados de acuerdo con la solicitud del cliente y que el producto final tenga una apariencia llamativa, ya que todos estos productos sean vuelto parte de nuestro entorno.
color en envase plástico, masterbatch, saturación de color en envase plástico